BY: SARNA SALZMAN
Jon Stimson is the Executive Director of Homestretch, a regional developer of affordable housing. He recently sat down with Sarna Salzman, SEEDS Executive Director and a Homestretch board member to talk about the Carver Street housing development project.
FIRST, HOW YOU DESCRIBE HOMESTRETCH AND ITS WORK?
Homestretch is a seasoned developer of affordable housing. We are dedicated to providing accessible
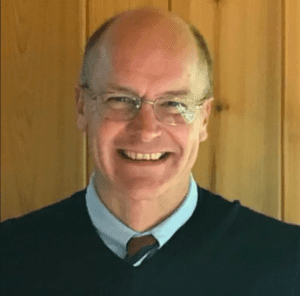
Homestretch Executive Director Jon Stimson
housing in this region and we do that by staying at the cutting edge of construction and development
technologies and tools. As a Community Housing Development Organization (CHDO), we are always
leveraging funding for projects and reducing costs wherever we can without detracting from the quality
of the homes we are building. This means we will take advantage of our low overhead, nonprofit tax
exemptions, solid trade relationships, and an evolving hybrid of modular construction techniques.
TELL US WHAT’S HAPPENING AT CARVER ST?
Across from DeWeese Hardware, we are building four 1-bedroom apartments (760ft2) and six 2-
bedroom units (920ft2) and each will house a family with incomes ranging from 60-80% of the area
median income. This project is currently under construction with occupancy expected before 2025.
“ Once you amortize
that $150/month utility bill over the life of the building, you’re talking about significant energy and
costs. We asked ourselves, why install that unrequired extra capacity? With current electric heat pump
technology, one utility source has become not only viable, but also sufficient."
— Jon Stimson, Homestretch Executive Director
WAS IT ORIGINALLY DESIGNED TO USE NATURAL GAS APPLIANCES?
That was the thought because that is the “normal” course of residential construction. We were,
however, enhancing the building envelope – adding insulation and additional air sealing – and halfway
through the project we realized that we could do away with a second utility source. The units
themselves are small and share some walls, so they will only require 8-10K BTUs to heat and cool; most
mechanical equipment in this country is sized for 24-30K BTUs. Because apartments are so compact and
utilities are so low, often no one cares enough to really think about utility costs. But once you amortize
that $150/month utility bill over the life of the building, you’re talking about significant energy and
costs. We asked ourselves, why install that unrequired extra capacity? With current electric heat pump
technology, one utility source has become not only viable, but also sufficient.
WHAT DOWNSTREAM IMPACTS DOES THIS CHANGE HAVE?
Once we eliminated the need for gas, we also eliminated the headache and cost of adding another piece
of equipment that only does one thing, provide heat, and we simplified the build-out process
considerably. Furnace installation is actually quite technical. Just welding pipe to
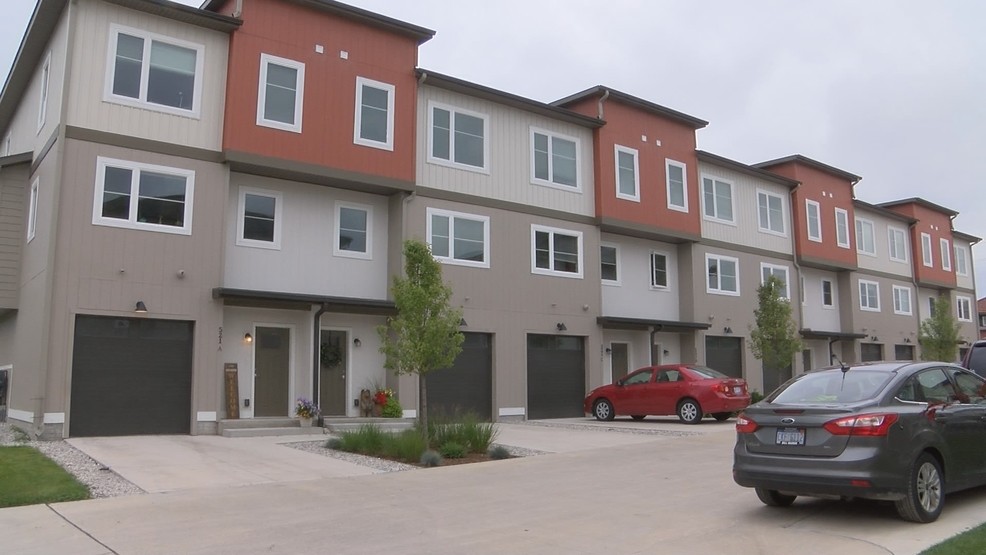
The townhomes on Depot Court are now filled with owners in after selling the 16th and final one in Traverse City. Photo by Up North Live.
contain gas requires skilled labor. Skilled trades are frequently unavailable and, when available, astronomically expensive given the current housing demand. The dollars saved on installation labor were then reallocated into making an even better building envelope. At Carver Street we have an extra $7K/unit going into the building envelope that will return a significant reduction in energy demand over the next 40-60 years. This is good for us, good for our environment, and great for our tenants. Another outcome is improved indoor air quality for our tenants. These units have no need for a carbon monoxide detection system because there’s no combustion pollutants in the house to mitigate. We also added Energy Recovery Ventilators (ERVs) to provide constant air monitoring and filtering, rather than only getting fresh air when the furnace is on. You have to import air to combust when a furnace is running, but when a furnace is off, indoor air contaminants spike unless you install additional equipment to control it. I would rather proactively handle air quality than rely on a ducted gas furnace.
ANY FINAL THOUGHTS YOU WANT TO SHARE?
Market rate is the easiest development you can do. What we’re doing is challenging and tough. We have
to be selective and detail oriented because there is just a limited supply of resources. It’s a grind, but I
like the sense of accomplishment knowing I’ve done something new and challenging that serves the
community.
For nearly 20 years, SEEDS has supported the development of quantified research and action plans that lead to:
- Energy Management for Cost Savings
- Energy Efficiency & Renewable Technology Developments